Shipping & Delivery: From Vermont to Your Door
It's true! We mill our flooring on the banks of the Connecticut River in Brattleboro, Vermont. Homeowners, businesses, and museums across the United States, Canada, and beyond have installed our custom-milled flooring and handmade stair parts. Our New England home gives us unparalleled access to the sustainably harvested trees we utilize for our products. Once our craftsmen mill those trees into beautiful, wide-width, hardwood flooring planks, we pack them with care and work with you to help prepare for delivery - wherever your neck of the woods may be.
Planning And Know-How
Moving hundreds of thousands of pounds of flooring safely and efficiently requires know-how and planning. But with 30 years under our belts, we've got it down to a science. When your floor goes into the final steps of the production process, your Production Coordinator reaches out to discuss the shipping schedule (and the coordination necessary) to prepare you for what’s required when working with private and common carrier services.
Carriers expect the recipient to unload the delivery from the truck. You may need to arrange for a crew of helping hands or even a forklift to move the flooring from the truck or curb to your job site. Your Production Coordinator will work through all these details with you (or with your builder), so you'll be totally prepared when your flooring arrives.
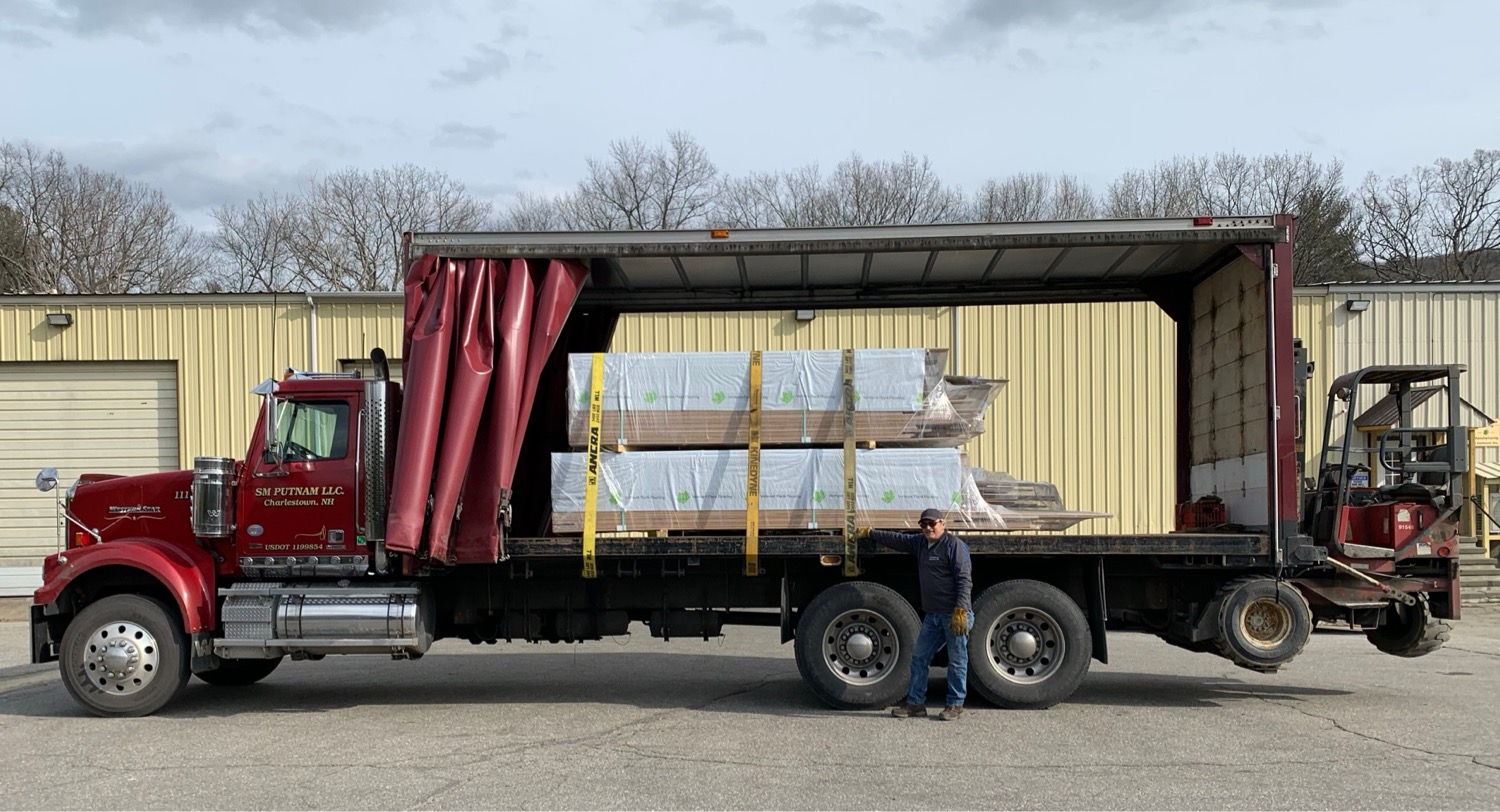
Packaging for Protection
Once your flooring project is complete, we'll carefully stack the planks on pallets, and package them labeled with your name and delivery notes for the trip.
Our packaging process takes into consideration the worst-case scenario. This is Vermont – New Englanders understand all kinds of weather conditions! We go to great lengths to protect your flooring from damage that can occur while in transit and from exposure to moisture. Orders are shrink-wrapped by hand and banded on pallets. Flooring orders sent by common carrier are wrapped and crated for protection as your packaged flooring moves through the terminal system.
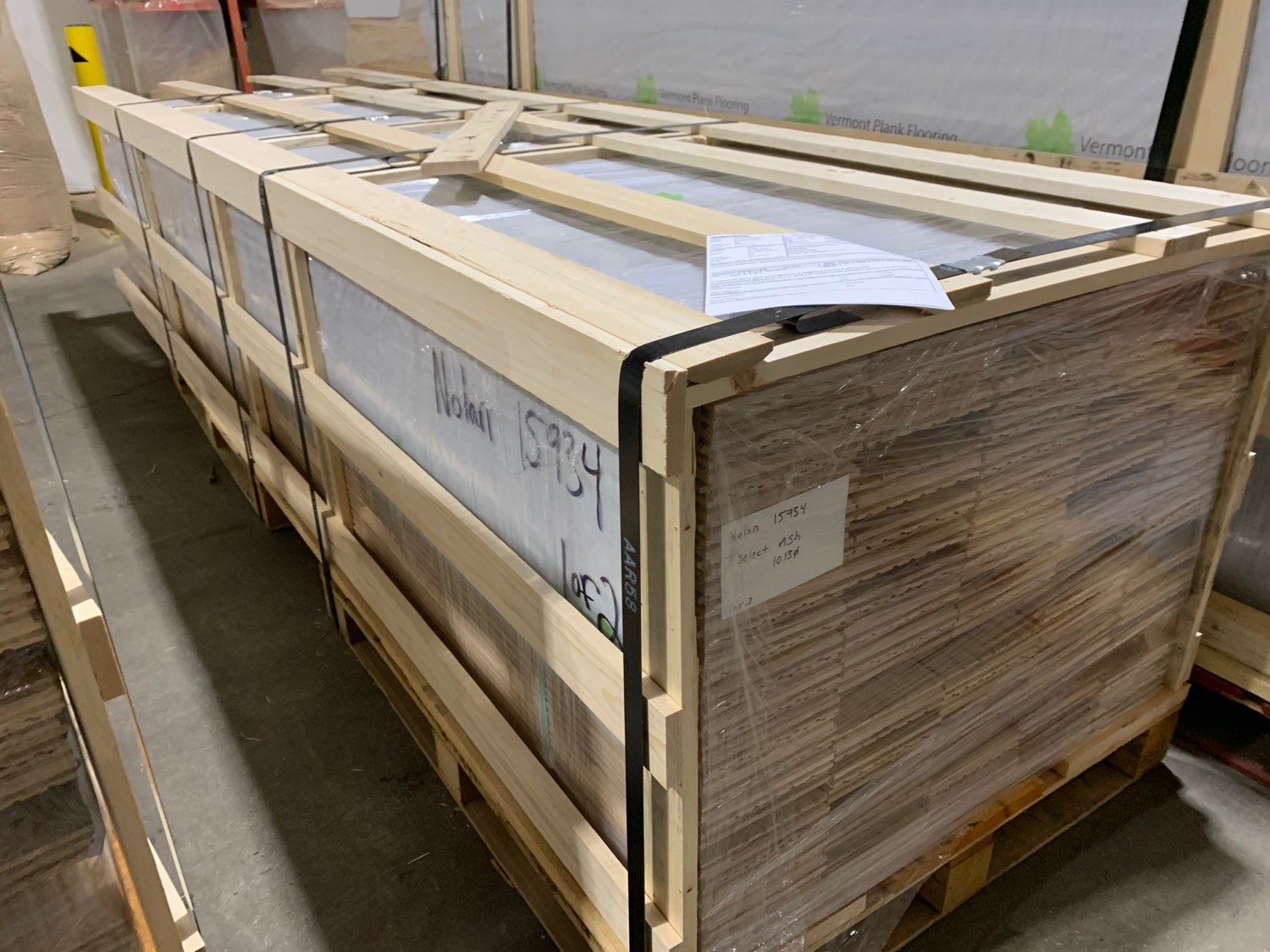
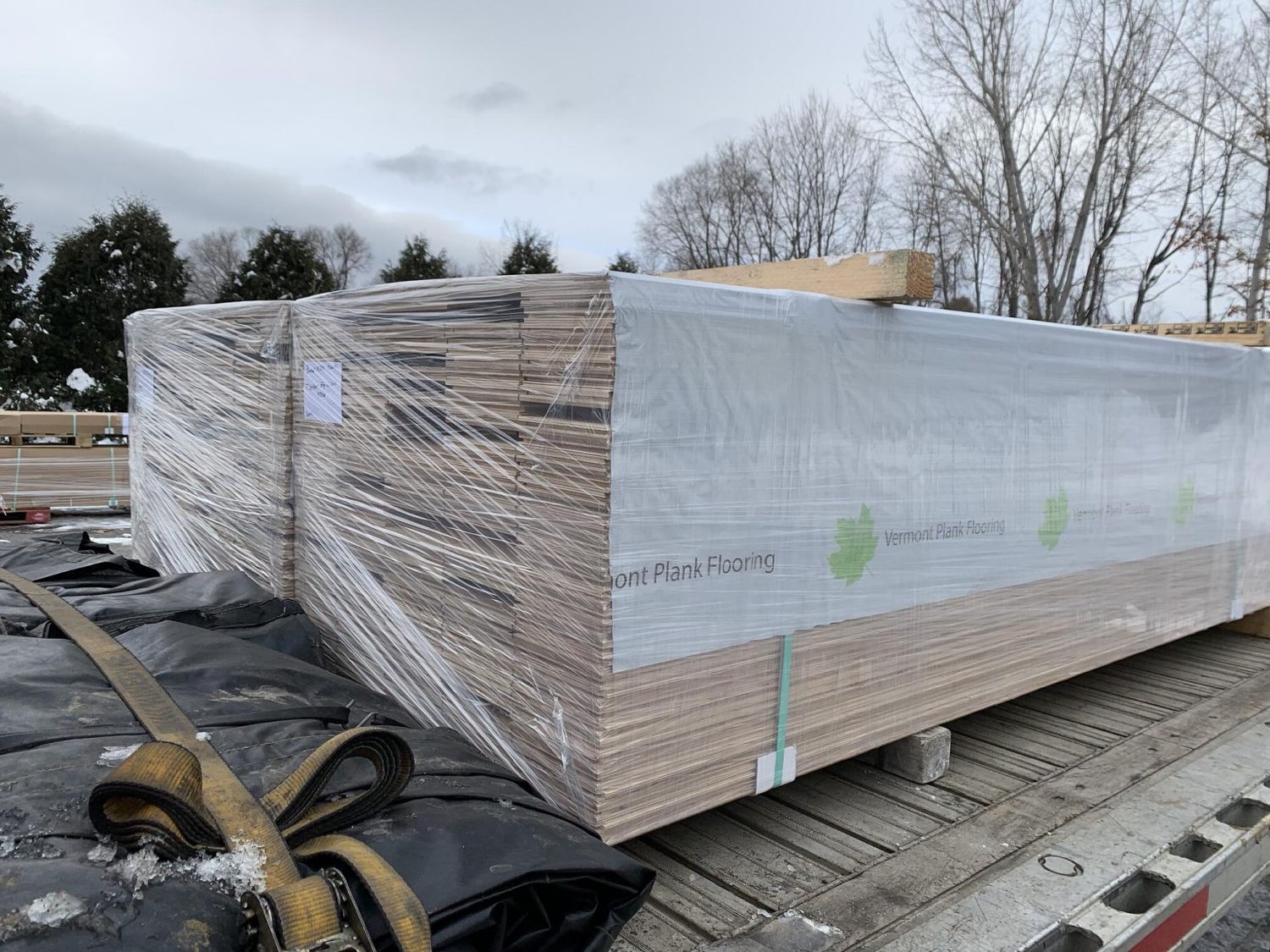
The Hand-Off
No matter where you're located, your Production Coordinator will work with you to confirm delivery dates and times or provide estimated arrival dates and tracking information for those working with common carriers. Having a crew ready to unload your order is essential for most deliveries in addition to having a dedicated acclimation-space cleared and prepared for the flooring, so you can get started right away. Review our Acclimation Guidelines and learn more about the science behind it here. As you stack your custom milled flooring to allow air circulation on all sides, you'll get your first tangible sense of the beautiful floor on which you will soon be walking! There is a little bit of Vermont in each of the projects we are proud to custom-mill for you.
👆 Courtesy of the geniuses @afterhoursfarm
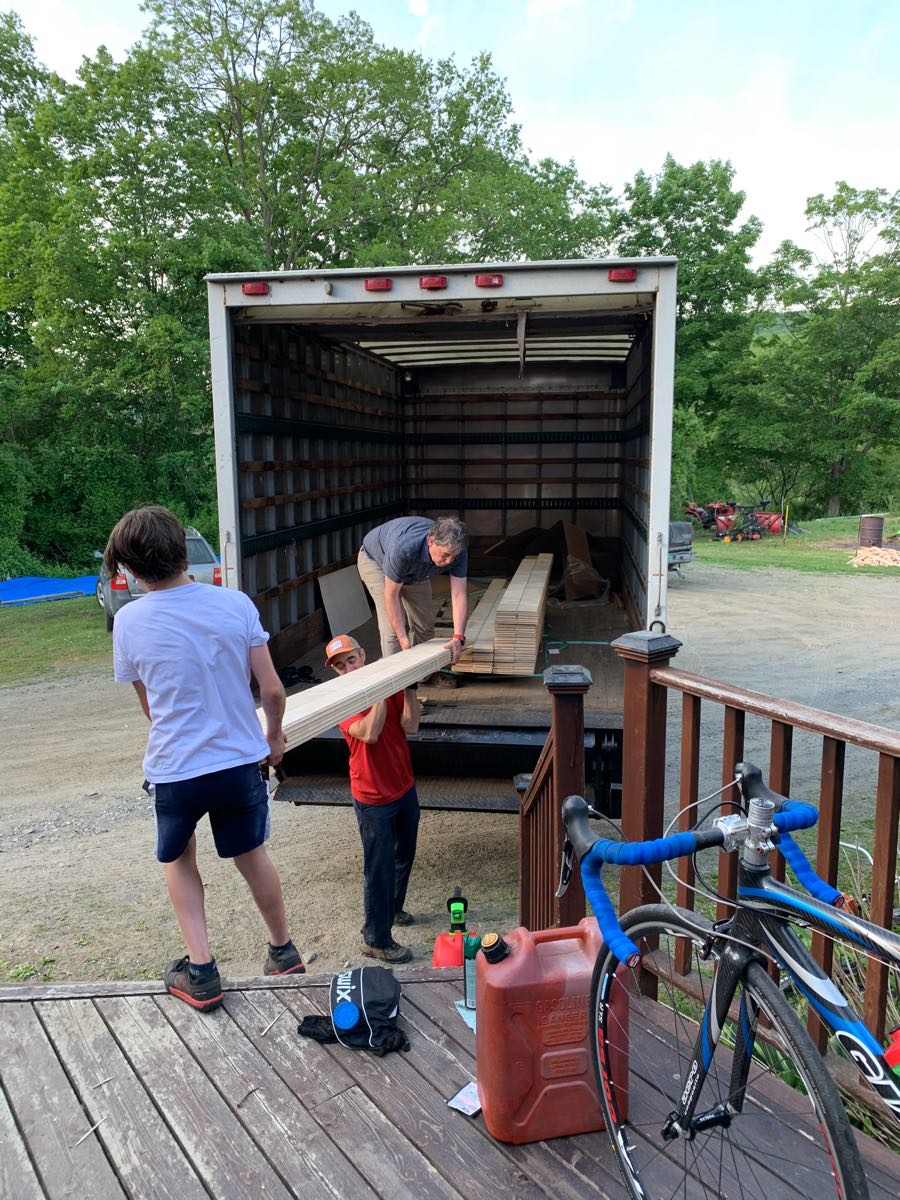
Unloading Engineered Maple Plank Flooring @westhillshop